Product Spotlight: PE-500 (Plus-E) All-In-One Vision System
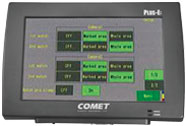
Don’t wait until it’s too late!
- Reduce costly mold damage and prevent lead-time delays.
- Improve mold cycle times by reducing ejection frequency.
- Detect shortages and burrs, preventing defective parts from mixing into the production line.
- I/O unit, main unit
- High-accuracy camera (with stand), plus, incandescent lighting fixture
- I/O cable set, and camera and interface cables (not shown).
Here are just a few of the advantages of the state-of-the-art vision system:
Easy Operation: Easily select setups and condition settings by using the simple touch panel display. The large, high pixel display enhances operational detail and convenience!
Compact & Lightweight: 25% smaller than previous models, yet larger LCD display making it easier to see and operate. Now weighing only 2 lbs., you can hold the unit with one hand while setting parameters or monitoring the screen with the other.
High Speed Image Processing: An exclusive high-tech calculator shortens capture time to just 0.03 seconds and data monitoring time to below 0.02 seconds. Shortening monitoring time reduces the production cycle, thus increasing capacity and significantly lowering total production costs.
Precise, Stable Monitoring: The high accuracy camera and 800×480 pixel display enables precise monitoring of even the smallest molded parts and the most intricate mold details. Unique compensation technology minimizes external light interference and machine vibration.
Two-Camera Monitoring: Since one unit can handle up to two cameras, you can monitor both the detail of multi-cavity small parts while also monitoring large-size molded parts.
External Data Storage: Easily store the setting conditions of each mold, monitor log data and capture NG images for later viewing onto a CF card. At your convenience, analyze the data and images to attain solutions for molding problems right on your PC.
For more information, call 800-328-5088 or email us at info@cometpe.com.